Synthetic graphite manufacturer Vianode has revealed its first high-performance battery solution derived from recycled graphite.
In a product brief, the company said that its recycled material shows the same cell performance and technical properties as non-recycled graphite. It also reportedly has the same charge rate performance as the reference material.
Graphite is the largest component in lithium-ion batteries, with each EV typically containing around 70 kilograms, and making up 25-30% of the battery in weight.
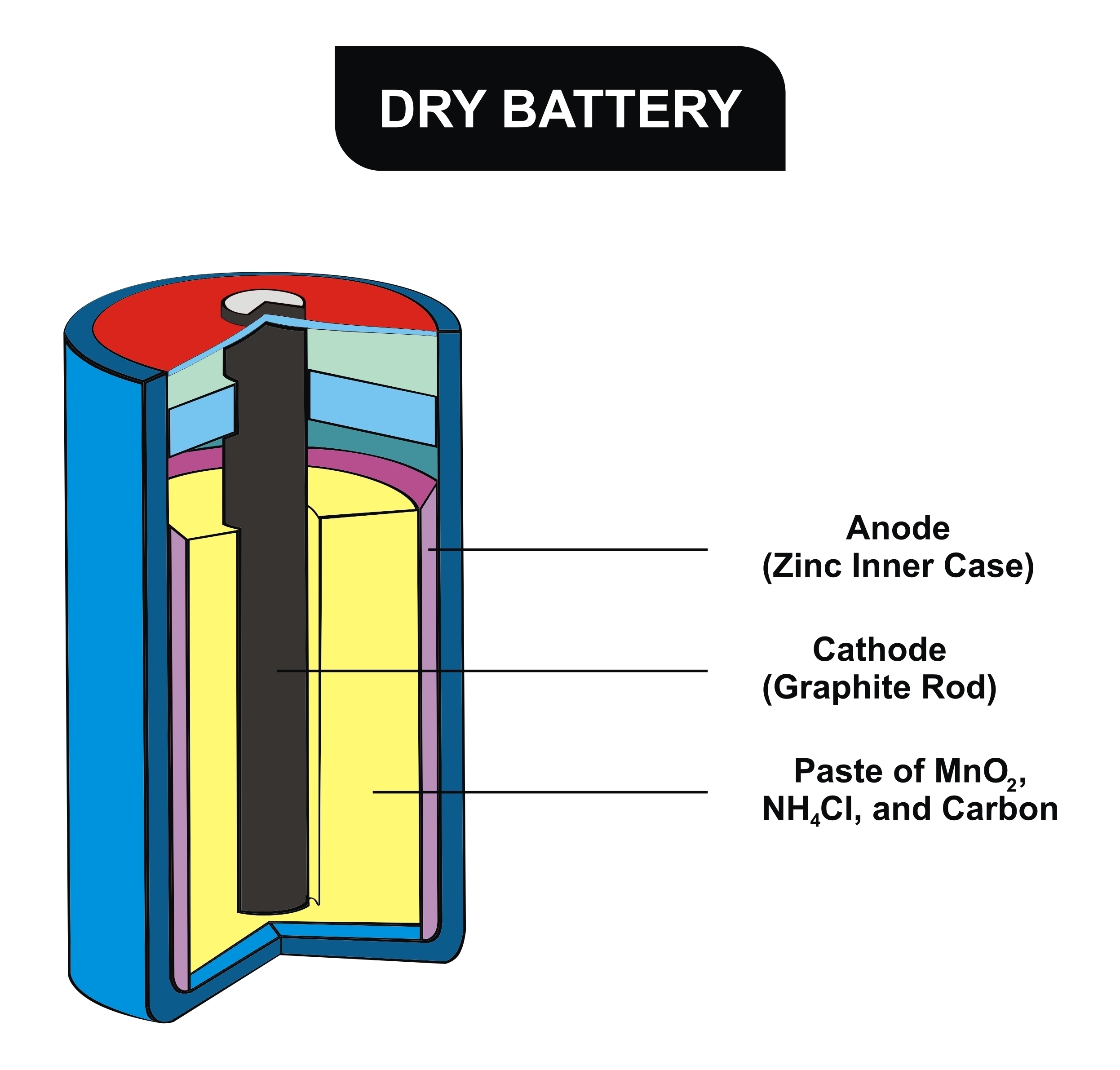
YOU MIGHT ALSO LIKE
According to clean technology company, Altilium, demand for graphite is expected to grow by 250% between 2023 and 2030, potentially leading to a global supply deficit of 777,000 tonnes by 2030.
As it stands, over 90% of the world's graphite is refined in China, which imposed export controls on graphite in 2023.
Battery production
According to Vianode, conventionally produced anode graphite accounts for approximately 20% of battery cell emissions, making recycling a priority for both those concerned with the environment and critical raw material supply.
"Our new recycled product completes the graphite loop in battery production, reducing reliance on virgin materials," Stefan Bergold, chief commercial officer at Vianode said.
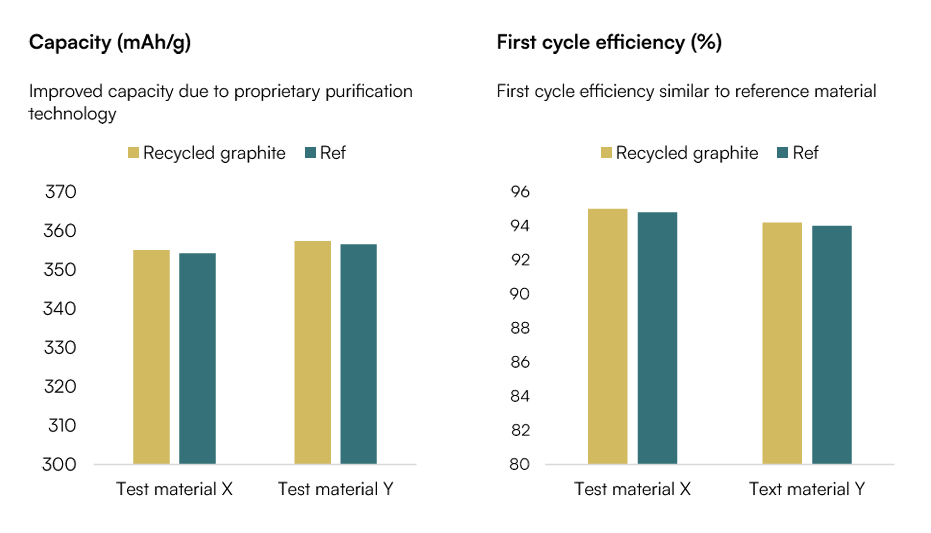
In North America and Europe, various regulatory initiatives are beginning to shape the graphite industry, particularly as countries seek to promote the use of domestic feedstock. Notably, the EU has set a target of achieving 25% recycling of synthetic graphite by 2030.
Graphite facility
Vianode's Via ONE plant, which commenced production in 2024, has been recognised as the world's most sustainable full-scale synthetic anode graphite facility. The plant boasts a record-low climate impact of 1.9 kg CO₂ equivalents per kilogram of graphite, representing a more than 90% reduction in emissions compared to conventional production methods.
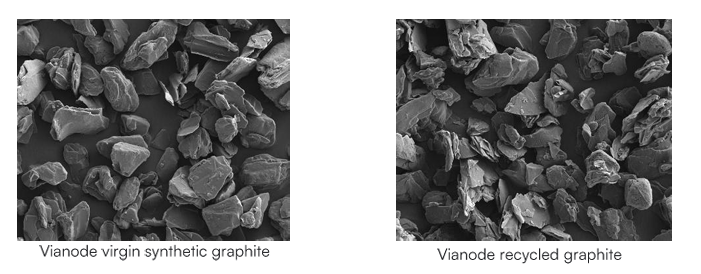
The company said that manufacturers can expect improved battery efficiency, including faster charging times and increased driving rang to meet the stringent performance standards of modern electric vehicles.
Anode materials in lithium-ion batteries typically consist of a mixture of synthetic and natural graphite. Vianode specialises in producing sustainable synthetic anode graphite through a proprietary high-temperature process. In contrast, natural graphite is mined from carbon-rich rock formations. Vianode's recycling process enables the recovery of both types of anode graphite.
The Vianode Technology Center in Kristiansand, Norway, is researching additional recycled products with the aim of creating the most sustainable form of anode graphite.
Broader trend
Vianode's initiative is part of a broader industry movement toward incorporating recycled materials in battery production. Earlier this year, Altilium, a UK-based clean technology group, announced a partnership with Talga Group to recover graphite from end-of-life EV batteries for reuse in new battery anodes.
Under a non-binding memorandum of understanding, Altilium proposed to supply Talga with up to 16,000 tonnes of recycled graphite over three years, commencing in 2026.
Altilium's proprietary EcoAnode process can recover over 99% of the graphite from end-of-life EV batteries. Initial tests have shown that this recycled graphite matches the purity and physical characteristics of primary sources.
The process has also been shown to deliver significant reductions in climate change impact for the production of anode materials, with 77% lower greenhouse gas emissions compared to primary production from China.
In a related development, General Motors (GM) entered into a multibillion-dollar agreement with Vianode to supply synthetic anode graphite essential for EV batteries. The material will be used in the production of next-generation EV batteries by Ultium Cells, GM's joint venture with LG Energy Solution.
Vianode plans to set up production facilities in North America, with shipments starting in 2027 and the agreement lasting until 2033.