Michelin has been clear on the challenge of sustainable tyre design. "Using recycled, sustainable or biobased materials in our tyres doesn't ensure that they're sustainable. They also need to have as little impact as possible on the environment throughout the entire lifecycle," Michelin Mining business segment manager and sustainability leader Lisa Hickey said.
But how does a company produce safe, sustainable, high-quality tyres that perform as well on a mining site as a Formula 1 racetrack? Central to Michelin's sustainability strategy is the adoption of the Life Cycle Assessment (LCA), a methodology standardised under ISO 14040-44. This tool evaluates the environmental impacts of products across their lifespan—from the extraction of raw materials to their end-of-life disposal.
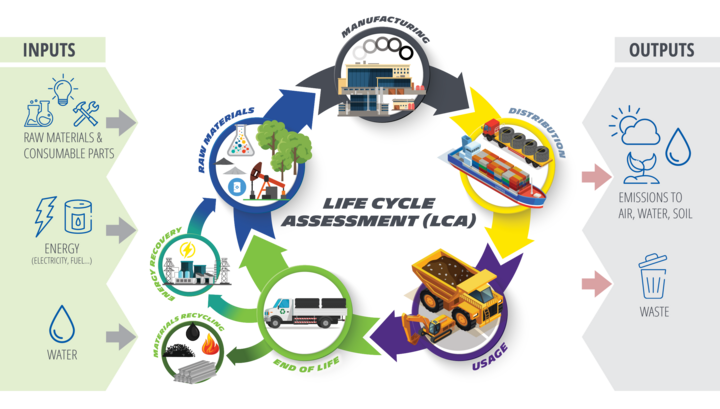
In one study in a copper mine in Chile, Michelin assessed the environmental impacts of the 53/80R63 MICHELIN XDR3 tyres equipped on 54 vehicles. It identified key areas for improvement without compromising tyre performance.
"We used the LCA tools to conduct a sensitivity study- examining each design factor to determine the net impact on the LCA score. The study revealed that decreasing the tyre motion resistance and increasing its load carrying capacity had the most significant impact on the environmental performance of the tyre," Michelin Mining research & development tyre designer and sustainability lead Virgile Ayglon said.
The LCA reflected that 70-90% of the environmental impact of tyres occurs during the usage phase. By decreasing motion resistance and increasing payload capacity, Michelin enhanced the vehicle's energy efficiency and contributed to lower operational costs and emissions for the mine. These findings have spurred Michelin to innovate tyres that not only last longer, but also enhance fuel efficiency without sacrificing performance.
Energy-efficient tyres reduce fuel consumption, which decreases carbon dioxide (CO2) emissions and air pollutants like nitrous oxide and sulphur oxide. "Consider a large open-pit copper mine in Chile, which typically consumes about 200,000 litres of fuel per day. Even a modest improvement in fuel efficiency, such as a 5% reduction, can substantially decrease fuel use—equating to 10,000 litres daily. This reduction not only offers considerable cost savings for the mine but also lowers emissions and pollution," said Ayglon.
Furthermore, optimising rolling resistance plays a crucial role in the transition to zero-emission vehicles, extending their range and enhancing productivity by reducing vehicle charging time. "The integration of energy efficiency into vehicle design is a pivotal component of the sustainable transition," said Hickey.
Michelin's proactive approach to sustainability through the use of LCAs not only addresses large-scale environmental challenges but also sets a benchmark for responsible industrial practices worldwide.
"Since 2023, one-hundred percent of our product launches must have an improved LCA score, with the ambition to extend this to services by 2025," said Ayglon. By 2030, Michelin has pledged that all new products will undergo LCAs to ensure continual environmental performance improvements.
This commitment is evident in their latest offerings, which are designed to carry heavier loads and move faster, thus enabling mining operations to achieve the same output with fewer vehicles and reduced CO2 emissions. Ayglon cites new products that maximised productivity and energy efficiency, including the XDR4 Extra Load and the XDR4 Speed and Speed + tyres, as well as, most recently, the 70/70R57 MICHELIN X MINE L4 tyre for large wheel loaders. "All of those products are showing breakthroughs in productivity and energy efficiency without compromising on wear," Ayglon said.
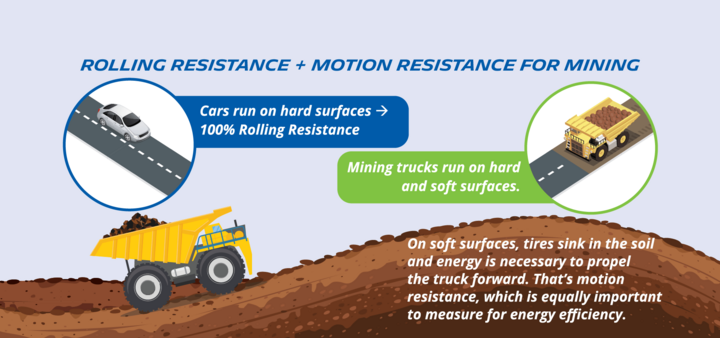
Meanwhile, Michelin is involved in cutting-edge projects that extend the boundaries of what's currently possible in sustainable tyre production. Michelin pledged to make its tyres entirely sustainable by 2050, with an ambitious interim goal of using 40% renewable and recycled materials by 2030. The company recently began construction on their first tyre recycling plant, which is based in Antofagasta, Chile, and aims to recycle 30,000 tons of earthmover tyres each year.
"The challenge is enormous, because it involves abating the impact of human activity on global warming while protecting the planet's resources and biodiversity. Industry-wide, this means replacing around two-thirds of the materials used today, which are derived from petrochemicals, with renewable or recycled materials. That requires structuring all the value chains, from collecting renewable primary materials and recyclable end-of-life tyres or other products to recovering any materials from them that could be reused in new tyres," Michelin research & development vice president Eric Phillippe Vinesse said in a report published in April 2024.
The commitment dares to achieve initiatives that reach beyond the confines of the automotive industry, using the science and innovation to drive changes necessary for a cleaner, more resilient future. This is important to a company that aims to strike a balance between people, profit and planet. "Michelin is not only transforming its products but also its processes and the industry standards around them," stated Hickey.